2K PRINTING UNIT - V7
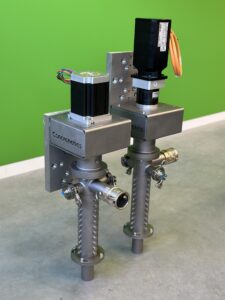
- Preassembled and packed. No installation. No integration.
What you get
1. Dynamic mixer - 2K print head
Servo motor
High power efficient servo motor, with variable frequency drive, gearbox, and torque feedback options
Mixing barrel
High shear mixing, with PU liner for easy maintenance, stator pins, and hardened rotor with carbide pins
Mortar flow inlet
Standard:
1 1/4″ or 1 1/2″ thread for M25 or M35 mortar coupling
Small volume inlets
multiple small volume inlets for: additives, accelerators, colorants / pigments and more…
Standard:
50.5″ tri clamp connections
to 8 or 12 mm tube inlets
Custom tool flange
Customizable hole layout to fit your end effector, portal frame structure, or more
End nozzle
Standard: Straight stainless steel nozzle of 40mm diameter
Cad files provided to create unlimited variations
2. Accelerator dosing pump
High precision dosing
Reliable 1.5 kW stepper motor with high torque at low speed
Excellent response to starting, stopping, speed changes
Low maintenance
Flush cleaning, can handle low to medium viscosity fluids with or without particles
Can handle aggressive suspensions (pH 0-14)
Pressure sensor
Optional: Pressure sensor, adjusted and adapted to fit the equipment and accelerator line
Measuring is knowing
Key features
Concrenetics’ 2K PRINTING UNIT packs all the components needed for 2K (or bicomponent) concrete printing at the end effector. It generally includes the latest generation of our in-house developed 2K inline mixing barrel, accelerator feeding system and other auxiliaries needed to transform a 1K print head to 2K.
The printing unit was optimized to be used with our own dedicated 3d-ink material formulation based on widely available raw materials and additives. However, other type of materials can be used, with aggregates sizes up to 2 mm in the standard rotor/stator pin configuration. The mixing quality was optimized to work with mortar flow rates between 5 and 10 L/min (and acc flow rates between 40 and 400 mL/min)
The key advantages of our system are high shear inline mixing with low torque requirements and allows for accelerated mix designs (with rapid vertical build rate, large overhangs…), aesthetic benefits like adding colours, or weight optimization (foaming agents) among others. The mixer is reliable, and easy to maintain due to the flexible liner on the inside. Furthermore, the system follows the KISS principle, is adaptable and can be integrated/expanded upon easily.
Dynamic mixer - end effector
- High shear inline mixing
- Multiple injection points
- Stress-tested / Certified
Accelerator dosing pump
- High precision dosing
- Low maintenance
- Pressure sensor included
Auxiliaries
- All components to transform 1K system to 2K
- Data monitorig and logging options
- Email support included
System specifications
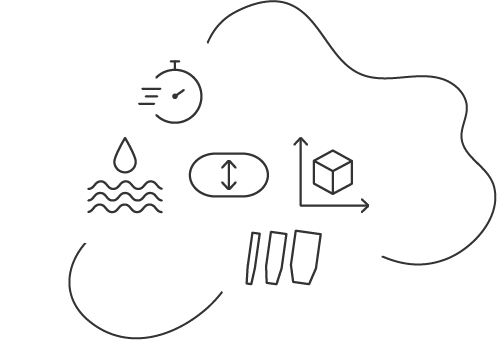
- Nozzle diameter 15 – 55 mm
- Optimal flow rate: 5 - 10 l/min
- Max printing speed 600 mm/s depending on nozzle size
- Maximum aggregate size: 2 mm